In 1990, Progressive Converting was established to fill a need for quick turn around, high quality sheeting in the Wisconsin market. Armed with a business plan and a Maxson sheeter, Progressive Converting began offering its services to the paper industry as a contract converter. Success soon followed and within a year, a second Maxson sheeter was installed.
Building on its reputation as a reliable supplier of sheeting, in 1995 Progressive Converting opened an eastern converting and distribution center near Hazelton PA. Positioning itself as an external converting supplier to paper mills, merchants and large sheet fed printers, Progressive Converting invested in state of the art equipment, adopted stringent quality control procedures, developed packaging capabilities that copied a mill’s finished product, computerized inventory control and warehoused roll stock to allow quick response.
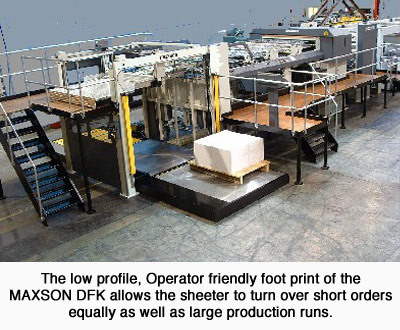
Continued growth led to a western US presence in 1998 with the launch of the Sparks NV facility.Progressive Converting enhanced its standing with their ability to sheet a wide range of substrates. Progressive Converting has also developed expertise in niche markets like synthetic paper and cut to registration of watermark and preprinted materials.
Quick to respond to emerging trends, the company helped major paper companies service the digital press size and small office/home office markets. Remarking on the digital sheet market, Vice President Norb Schreiber notes, “It’s a tough market because the tolerances are more critical and there are lots of size changes and different substrates. Pro Con has done pretty well and we believe that market will continue to grow.”
Today Progressive Converting employs over 200 people among their three locations, with five sheeters and a rewinder in Appleton WI, three sheeters and a rewinder in Hazelton PA, and two sheeters in Sparks NV. The company continues to hold true to its model of responding to the needs of the Customer with a quality product in a timely, cost efficient manner using state of the art technology. The company’s most recent investment is an example of their commitment.
During 2002, Progressive Converting’s Appleton WI facility was operating at full capacity and finding it difficult to schedule more business. As Norb Schreiber relates, “We were running 7 days a week, 24 hours a day and working our employees very hard. Based on that we decided to purchase a new sheeter.”
Consistent with Progressive Converting’s philosophy, an investment in sheeting equipment required that it be state of the art and of modern technology, but with a reliance on the Operator to maintain strict quality control. “Automation is wonderful,” observes Schreiber, “but it cost money. “Although it takes one less human factor out of the equation, by the same token we rely on our operators to maintain a level of quality. Some automation we don’t feel is necessary and we elect not to put it on the machinery.”
The process of selecting a sheeter involved soliciting bids from equipment manufacturers. The primary consideration was insuring that the proposed machinery could convert the wide range of materials that Progressive Converting needed to sheet. Said Schreiber, “We run 24# bible paper up to 36 point board, and we are not bashful or shy about running any of it. When we buy sheeters around here, we want the equipment to run a wide range of materials.”
After visiting other sites to see the various offerings and reviewing the pricing, Progressive Converting chose a Maxson DFK Sheeter. “We felt comfortable we could run board down to light weights on the Maxson sheeter.
The DFK Sheeter was outfitted with five shaftless roll stands, each outfitted with individual tension control and motorized decurlers capable of handling rolls up to 72” diameters. A splice detector, programmed to divert splices at the sheeter’s reject gate, insured no bad sheets reached the pile.
Progressive Converting elected a dual slitting rig with digital read out positioning. Says Schreiber, “I think when it comes to a dual slitting station, that’s a feature we really like, because when we are running certain grades up to 0.014” thick, we can put a web through each slitter. If you are 60# label paper, we can run three webs through one set of slitters and two webs through the other, which results in better quality.”
The cutting section uses a dual rotary knife design and is equipped with dual AC motor technology. “The machine is very accurate and sheet length is very important. You also get a good quality cut which is equally important”, declares Schreiber. “It has to cut accurate and clean.”
The sheeter is also outfitted with a non stop, rapid pallet discharge system that allows continuous operation with out the loss of any sheets during pallet changes. At a preset count, the full pallet is lowered and moved off line while an empty skid is raised into place. “The shuttle discharge is important because we get paid for the material we produce, so there is less waste when there is no dumping material on the floor. The discharge system is efficient and works well for us”, reports Schreiber.
The installation of the sheeter and the training of operating crews went smoothly according to Schreiber. “The sheeter was shipped between Christmas and New Year’s Day. It was installed in a couple of weeks, followed by two weeks of training. By the end of January it was running in production.”
Schreiber also noted the DFK Sheeter’s simplicity of design and machine profile. “From a maintenance standpoint we feel very comfortable addressing the mechanical and electrical components. The drive system has been dependable. And with a US manufacturer, anything close to home is better for service and repair parts.
Concludes Schreiber, “The user friendly design provides us with the ability to set up the sheeter on most grades in an acceptable time and change over times meet our schedules, while maintaining our quality standards. This machine keeps it simple and straightforward. We are certainly happy with what we have.”
Investing in such converting equipment has assured Progressive Converting’s success in its objective to help paper mills address the challenges of efficiently meeting the needs of printers demands in today’s quick delivery, challenging environment
Reprinted from Converting Today, February 2004
Building on its reputation as a reliable supplier of sheeting, in 1995 Progressive Converting opened an eastern converting and distribution center near Hazelton PA. Positioning itself as an external converting supplier to paper mills, merchants and large sheet fed printers, Progressive Converting invested in state of the art equipment, adopted stringent quality control procedures, developed packaging capabilities that copied a mill’s finished product, computerized inventory control and warehoused roll stock to allow quick response.
Continued growth led to a western US presence in 1998 with the launch of the Sparks NV facility. Progressive Converting enhanced its standing with their ability to sheet a wide range of substrates. Progressive Converting has also developed expertise in niche markets like synthetic paper and cut to registration of watermark and preprinted materials.
Quick to respond to emerging trends, the company helped major paper companies service the digital press size and small office/home office markets. Remarking on the digital sheet market, Vice President Norb Schreiber notes, “It’s a tough market because the tolerances are more critical and there are lots of size changes and different substrates. Pro Con has done pretty well and we believe that market will continue to grow.”
Today Progressive Converting employs over 200 people among their three locations, with five sheeters and a rewinder in Appleton WI, three sheeters and a rewinder in Hazelton PA, and two sheeters in Sparks NV. The company continues to hold true to its model of responding to the needs of the Customer with a quality product in a timely, cost efficient manner using state of the art technology. The company’s most recent investment is an example of their commitment.
During 2002, Progressive Converting’s Appleton WI facility was operating at full capacity and finding it difficult to schedule more business. As Norb Schreiber relates, “We were running 7 days a week, 24 hours a day and working our employees very hard. Based on that we decided to purchase a new sheeter.”
Consistent with Progressive Converting’s philosophy, an investment in sheeting equipment required that it be state of the art and of modern technology, but with a reliance on the Operator to maintain strict quality control. “Automation is wonderful,” observes Schreiber, “but it cost money. “Although it takes one less human factor out of the equation, by the same token we rely on our operators to maintain a level of quality. Some automation we don’t feel is necessary and we elect not to put it on the machinery.”
The process of selecting a sheeter involved soliciting bids from equipment manufacturers. The primary consideration was insuring that the proposed machinery could convert the wide range of materials that Progressive Converting needed to sheet. Said Schreiber, “We run 24# bible paper up to 36 point board, and we are not bashful or shy about running any of it. When we buy sheeters around here, we want the equipment to run a wide range of materials.”
After visiting other sites to see the various offerings and reviewing the pricing, Progressive Converting chose a Maxson DFK Sheeter. “We felt comfortable we could run board down to light weights on the Maxson sheeter.
The DFK Sheeter was outfitted with five shaftless roll stands, each outfitted with individual tension control and motorized decurlers capable of handling rolls up to 72” diameters. A splice detector, programmed to divert splices at the sheeter’s reject gate, insured no bad sheets reached the pile.
Progressive Converting elected a dual slitting rig with digital read out positioning. Says Schreiber, “I think when it comes to a dual slitting station, that’s a feature we really like, because when we are running certain grades up to 0.014” thick, we can put a web through each slitter. If you are 60# label paper, we can run three webs through one set of slitters and two webs through the other, which results in better quality.”
The cutting section uses a dual rotary knife design and is equipped with dual AC motor technology. “The machine is very accurate and sheet length is very important. You also get a good quality cut which is equally important”, declares Schreiber. “It has to cut accurate and clean.”
The sheeter is also outfitted with a non stop, rapid pallet discharge system that allows continuous operation with out the loss of any sheets during pallet changes. At a preset count, the full pallet is lowered and moved off line while an empty skid is raised into place. “The shuttle discharge is important because we get paid for the material we produce, so there is less waste when there is no dumping material on the floor. The discharge system is efficient and works well for us”, reports Schreiber.
The installation of the sheeter and the training of operating crews went smoothly according to Schreiber. “The sheeter was shipped between Christmas and New Year’s Day. It was installed in a couple of weeks, followed by two weeks of training. By the end of January it was running in production.”
Schreiber also noted the DFK Sheeter’s simplicity of design and machine profile. “From a maintenance standpoint we feel very comfortable addressing the mechanical and electrical components. The drive system has been dependable. And with a US manufacturer, anything close to home is better for service and repair parts.
Concludes Schreiber, “The user friendly design provides us with the ability to set up the sheeter on most grades in an acceptable time and change over times meet our schedules, while maintaining our quality standards. This machine keeps it simple and straightforward. We are certainly happy with what we have.”
Investing in such converting equipment has assured Progressive Converting’s success in its objective to help paper mills address the challenges of efficiently meeting the needs of printers demands in today’s quick delivery, challenging environment
Reprinted from Converting Today, February 2004